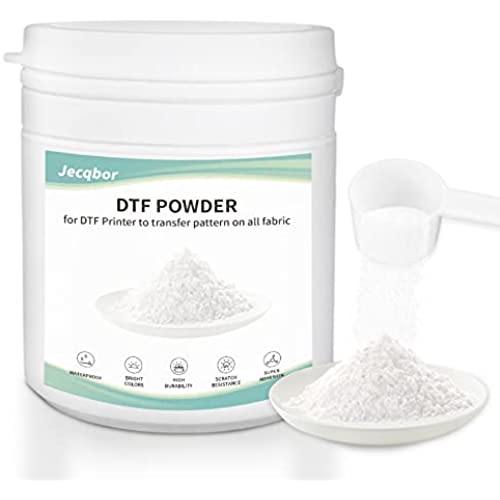
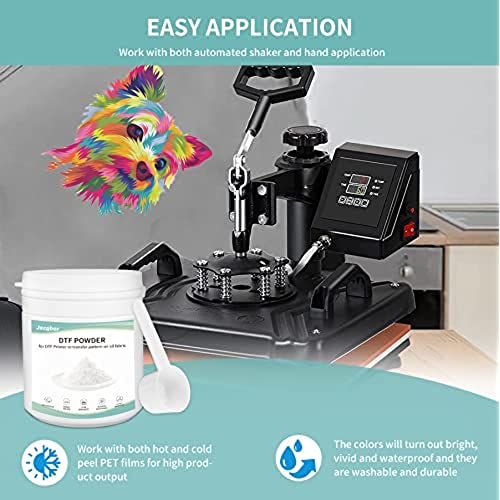
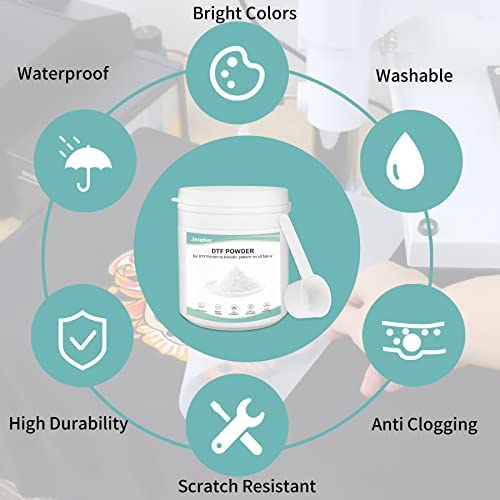
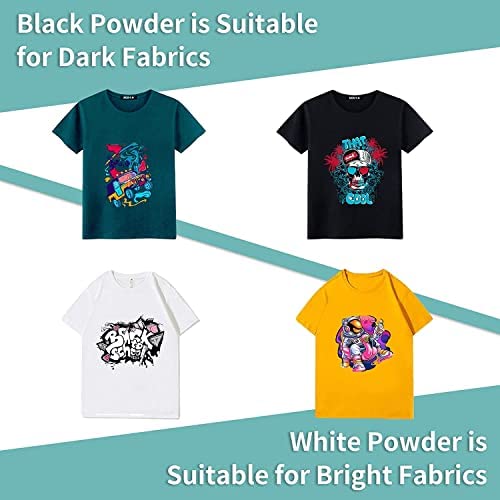
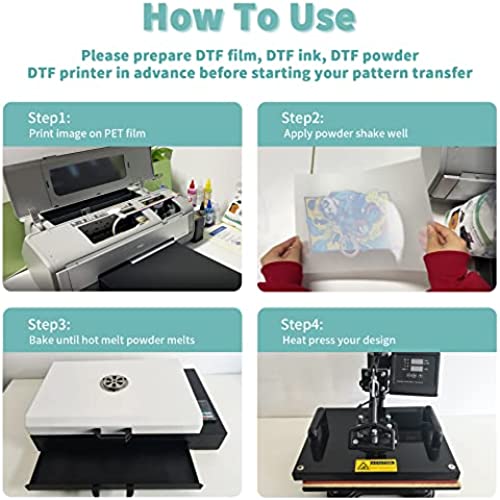
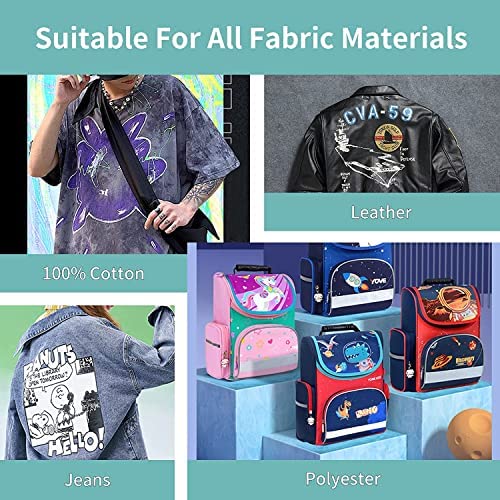







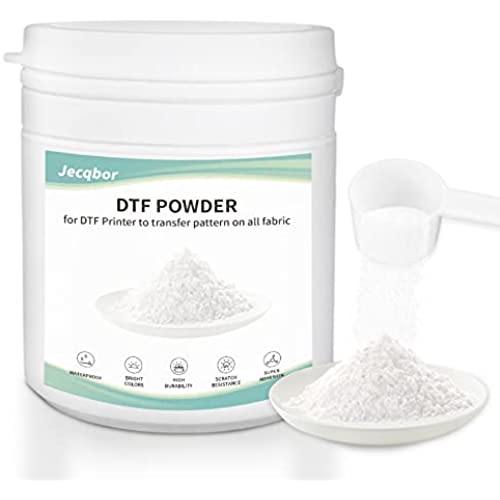
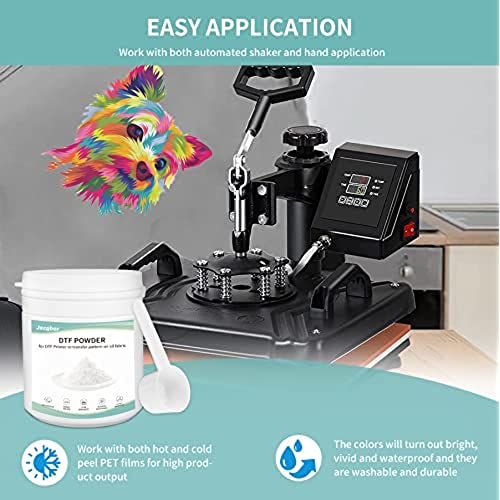
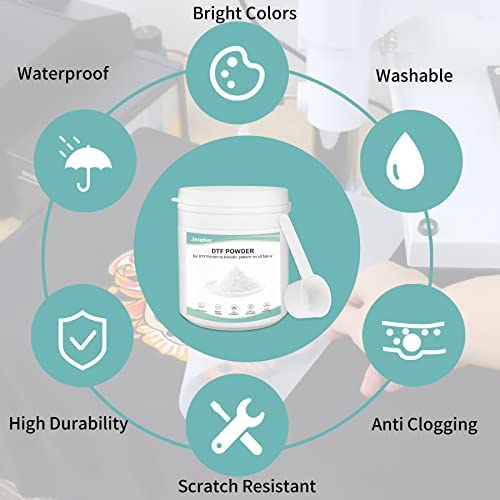
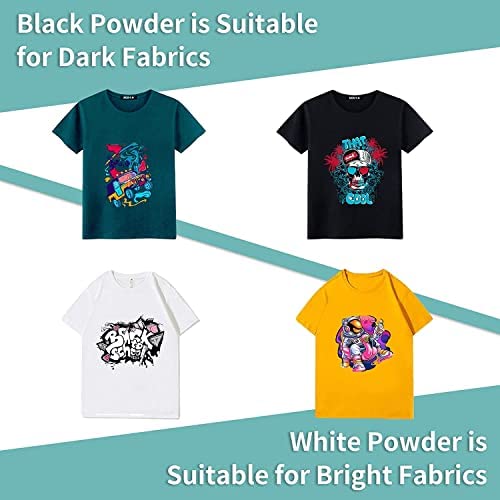
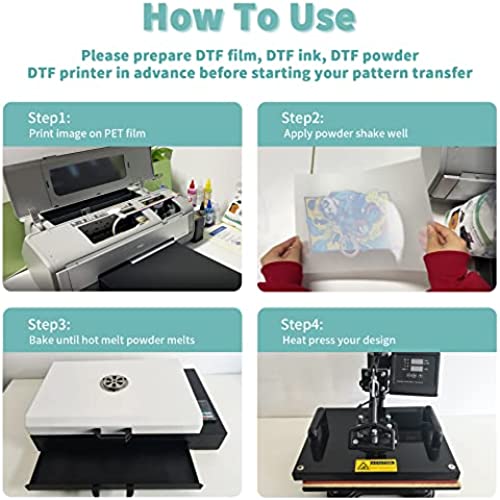
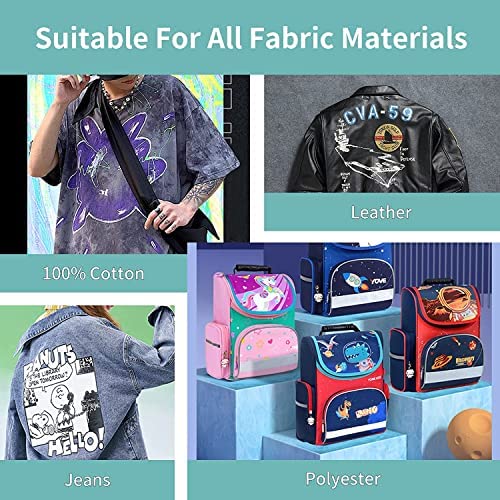







Jecqbor DTF Powder White Digital Transfer Hot Melt Adhesive, 400g/14oz DTF Pretreat Powder for DTF Printer Direct Print on All Fabric Include Jeans Cotton T Shirt Textile etc
-
Ashley Sabath
> 24 hourAfter accidentally becoming the owner of a heat press I decided sublimation and dtf transfer ought to be my newest hobbies. Therefore I ordered this powder and it’s black counterpart after reading dtf powder was a necessary tool. Unfortunately I have only used one other kind before- my frame of reference is rather small. But I will say it does work. My images adhered to the fabric. However, I can’t say whether it worked well for sure. I think the first one I used worked marginally better. This product was also less expensive and a little of it went a long way so this bag will last me awhile.
-
tmax
> 24 hourI love how easy and fast it melts and the adhesion is crazy good and theres no cracking after washing the tshirt several times I really like this dtf powder. Very easy to use it sticks to the ink great and setting it is quick and extremely easy and I just love how the image transfers it sticks so well theres no part of the image that doesnt stick to the cotton shirt I love it. Very affordable and when dealing with anything dtf it can get expensive so I love when things that pertain to my hobby are affordable.
-
Cupcake
> 24 hourDTF Transfer Film Paper PET Heat Transfer Paper A4 (30sheet), Double-Sided Glossy Clear Pretreat DTF Film for DTF Epson Inkjet Printer, Direct Print On T-Shirts Textile (8.3 x 11.7) I don’t have a proper DTF printer or inks, but I do have an inkjet printer and an Epson Ecotank loaded with sublimation inks, and I saw a number of youtube videos about doing bootleg DTF, so I decided to give it a go! Bottom lining it: with some trial and error, you can get pretty great DIY results using this product with sublimation or inkjet inks. In my experience, the sublimation ink produced a better print, but the inkjet did work. I also just want to caveat this with the expectation that these are very nice DIY results, but I wouldn’t put myself out there as a professional, because I don’t know how well the bootleg results would last over time. I’m using this for my own shop promo products that I wanted to print on cotton, not items I’m selling. And I’m not printing on anything that will be laundered or take the abuse that garments or a heavy-duty item would. I would not feel comfortable selling transfers without some serious trial and error. That said, I’m really happy with my DIY results, which look much better than your typical inkjet iron-on transfer material and have a lot more detail than my cricut/htv options (and a lot less time/work). And unlike straight sublimation, this works on cotton. But I am not a professional printer and can’t rationalize buying a proper DTF printer just for my occasional promo items, so these are purely DIY level results. I’d still go with a pro if I needed a large run or garments, but for small runs of promo items and one-off custom items for personal use, yay! So, if youve done this before and you just want to know if this product does what its supposed to do, Id say yes. If you want more details on trying it for DIY projects, read on... I used this film with a random brand of powder. Based on this, and the fact that this paper/film explicitly said it *wasn’t* for inkjet or sublimation inks, but ended up working, you might be able to get most random combos to work successfully with some trial and error. First of all, my powder didn’t include any instructions, so I got my info from you tubers and Professor Google. This paper includes instructions, but they were for a professional setup, and didnt so much apply to me. Which is to say, I did what the said not to do. :) Challenges with printing with a regular printer: Mirror/Reverse/Flip horizontally: If your printer doesn’t have this setting, you’ll need to mirror the original art. Feeding: DTF paper is slick and a regular printer isn’t designed to handle this substrate, so you’ll probably have problems (one printer jammed, another picked up the paper but would only print a couple of lines before stopping). I put a strip of washi tape across the top on the slick (non-printing) side and that was enough for two of my printers to grab it; the third would only grab it when I taped a sheet of copy paper to the slick side Streaks: Use standard print (not high quality) to minimize streaks. Experiment until you get as clean a print as possible. My ET-4750 (regular inkjet ink), which uses dye-based inks (not pigment-based) had the most trouble (both with feeding and a clean print). My WF-7720 made the cleaner print of the inkjets. Color: Both inkjets produced brighter colors than the sublimation inks, but the sublimation ink did really well with the white portion of the design, which was just clear/fabric color with the inkjet Coating the wet print with powder was straightforward—just sprinkle the powder over the wet print, then move the page side to side so the powder flows across it evenly, then tap off the excess. The printing will look like it’s coated with a fine layer of fine sugar. You can keep reusing the excess powder. I use a small jar to pour the powder and a letter-sized plastic bin, and afterwards pour the excess back into the jar. Challenges with curing (the trickiest step): Heat press: While pros seem to cure with a hovering (not closed) heat press or specialized oven, my budget press wouldn’t cure the powder. Maybe I wasn’t hovering close enough to do the job, but the teflon fabric on the top of my press is saggy. (If your heat press is better than mine, the suggestion seems to be about 2 minutes at 325F.) Then I tried an old toaster oven with varying results. Try about a minute or so at 150. All this is going to vary with the peculiarities of your own oven, so youll need to experiment. Keep in mind this does produce fumes—nothing scary if you’re only doing a sheet or two, but you’ll definitely need ventilation if you cure more than that. Further, I wouldn’t do this with a toaster over you’re cooking in. When its done curing, it will look glossy, and be continuous with an orange peel appearance rather than a dry grainy appearance. Pressing: This was fairly straightforward. Working on 100% cotton muslin and canvas, I used my heat press at 325F, did a 15-second pre-press, a 15 second press covered with parchment, then a cold peel to remove the film, and another 15-second press with parchment. Voila! Dont skip that final press--its critical for getting the transfer to soak in so you dont have any visible edges. Results: While I liked the more vibrant look of the inkjet results, you can’t beat the white results with the sublimation ink (to be clear, it doesn’t print white, but the actual pale gray of the white does print in all formats—it’s just that perhaps something about the sublimation ink binds better with the powder to produce a better “white” effect in the final result? Conclusion: If you have an inkjet or sublimation printer, give it a whirl! Do know that you might waste a lot of paper before you get good results, but it’s a lot better looking and versatile than old-skool inkjet transfer paper.
-
Casani
> 24 hourUsed this as soon as it arrived to print transfers for onesies. Great job and looks wonderful!
-
Parker-Moore and Family
> 24 hourWe have a DTG printer so experimenting with the DTF applications with Transfer Film A3(11.7 x 16.5”) Double-Sided Matte Clear and (8.3 x 11.7) Double-Sided Glossy finish. I am leaning toward the matte clear finish sheets since our printer seems to not like the glossy paper as much, it’s a printer issue not the paper. Both work great, just matte works better for our old printer. When we upgrade the printer I’m sure the glossy film will work better.
-
Aubree Price
> 24 hourWorked out with my sublimation printer. had no issues at all with printing
-
Fiorella
> 24 hourEasy to use! Looks great on my prints! Love it!
-
Keep Smyelin :)
> 24 hourGreat item - exactly as described. :)
-
Sara
> 24 hourThis is the best powder Ive used. Super fine!
-
Melissa P
> 24 hourWorks well and holds up to washes.